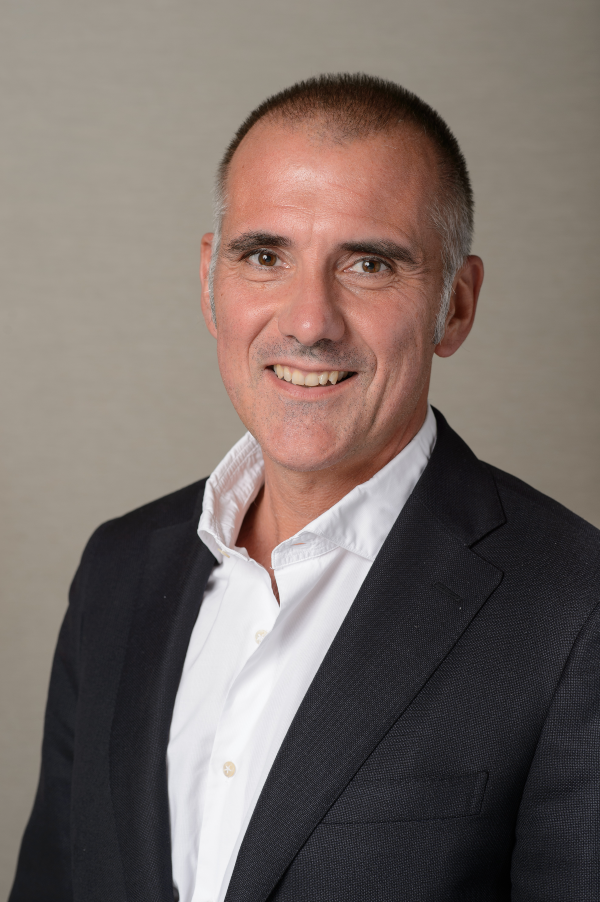
Nel settore manifatturiero, i dati sono dappertutto. La rapida adozione di sensori e dispositivi connessi ha infatti portato a una proliferazione dei dati generati nell’ambiente manifatturiero. Tali dati possono essere di vario tipo: dati macchina, di qualità, di processo, relativi ai materiali. E questo nei soli reparti di produzione. In ogni azienda, tuttavia, esiste una miriade di altri sistemi che forniscono informazioni relative alla supply chain, al reparto finanziario, all’assistenza e, nel caso dei prodotti smart, anche relative a feedback dai clienti.
Questi big data sono essenziali per aumentare la produttività, migliorare l’efficienza e scoprire nuove idee che possano promuovere l’innovazione. Grazie all’analisi dei big data nel settore manifatturiero, le aziende possono quindi scoprire nuove informazioni e identificare dei modelli che permetteranno loro di migliorare i processi, incrementare l’efficienza della supply chain e identificare le variabili che incidono sulla produzione.
Il PLM come spina dorsale digitale
Secondo lo studio “The State of BI, Data and Analytics in Manufacturing” recentemente pubblicato da Dresner Advisory Services, l’89% delle aziende che hanno avviato progetti di analisi e business intelligence (BI) li considera iniziative di successo, tanto da aver permesso loro di sopravanzare i concorrenti in settori analoghi. Inoltre, il 49% delle aziende prevede di aumentare anno su anno i propri budget dedicati all’analisi e alla BI. Infine, il 62% delle aziende del settore manifatturiero intervistate afferma che la BI è stata essenziale per le loro attività nel 2020.
Da tempo abbiamo capito che i dati fanno la differenza fra un’azienda competitiva e un’azienda non competitiva. Un produttore o un team di ingegneri che non hanno il controllo dei propri dati o che non generano e acquisiscono i dati corretti, vedranno diminuire le possibilità di innovazione e di operare con efficienza, sia internamente che con il loro prodotto.
Come gestiscono le aziende questa grande quantità di dati preziosi? La spina dorsale della loro acquisizione dati è il sistema PLM e oggi vi è una significativa consapevolezza delle sue capacità all’interno delle imprese nel settore manifatturiero, che si stanno attrezzando con strutture digitali in modo da poter disporre di una visione delle informazioni di prodotto anche da una prospettiva ingegneristica, parte fondamentale dei concetti di trasformazione digitale e digital thread.
I sistemi PLM non sono una novità nel settore manifatturiero. Molte aziende hanno iniziato il loro percorso PLM dieci o anche 15 anni fa, ma sanno che c’è ancora molto lavoro da fare prima di ottenere il controllo dei dati di cui hanno bisogno. Gli investimenti nel PLM stanno crescendo in modo significativo ed è cruciale che questa spina dorsale sia adatta all’azienda perché, in caso contrario, il futuro dell’azienda stessa potrà diventare sempre più complesso.
Il valore di un ambiente dati comune
Nell’ambiente della fabbrica connessa, raccogliere i dati tipicamente non è un problema. Tuttavia, organizzare e combinare i dati in modo che diventino utili e significativi, permettendo all’impresa di utilizzarli per agire o prendere decisioni, è sempre stato problematico.
La difficoltà consiste nel raccogliere i dati da fonti diverse in un ambiente eterogeneo. Il problema esiste da molti, molti anni. Nei reparti di produzione nel settore manifatturiero si generano una grande quantità di dati, ma estrarli, combinarli con i dati aziendali e unirli ai dati PLM ed ERP non è facile. È difficile ottenere informazioni da livelli di sistema differenti in modo da poterle integrare tutte insieme.
Un’altra complessità nell’enigma dei dati è costituita dai cosiddetti dati oscuri. Molti dei dati raccolti risiedono infatti in enormi bacini che spesso non sono altro che un terreno di deposito senza alcuna struttura. Ciò rende difficile per il team di business intelligence estrarre qualsiasi valore. È necessario entrare, scoprire che cosa si sta cercando e mettere insieme le informazioni. In quasi tutte le aziende vi sono oggi dei reparti che hanno il compito di fare questo lavoro. Questo volume di dati non facilmente analizzabili può intaccare la capacità di svolgere rapide analisi, impedendo così di prendere le decisioni migliori per l’azienda.
D’altro canto, sia che ci si orienti verso l’AI o il machine learning, generalmente più dati si hanno e più opportunità nascono, purché si abbia a disposizione la potenza di calcolo per elaborarli. Più dati si hanno, più è probabile che si riescano a stabilire dei pattern e un modello affidabile di machine learning con i quali gestire la propria azienda nel settore manifatturiero da un punto di vista predittivo o prescrittivo.
La via verso i dati di valore
Quando le aziende mi chiedono come dovrebbero approcciare i loro dati, rispondo che una corretta gestione dei dati deve seguire tre direttrici: la trasformazione digitale, la fabbrica connessa e il prodotto connesso.
La trasformazione digitale si basa su un thread digitale all’interno della propria azienda nel settore manifatturiero, che poggia su tre pilastri che rappresentano le sue tre fonti primarie di informazione. Il primo è l’ingegneria connessa, l’ambiente PLM. Esso comprende dati dettagliati di prodotto, dati della supply chain, informazioni di produzione e dati di qualità.
Vi è quindi la fabbrica connessa, che spinge tutti i dati dei reparti di produzione a un livello superiore nella propria azienda, rendendoli accessibili e visibili.
Il terzo pilastro è il prodotto connesso. La ricca fonte di informazione su ciò che sta accadendo al prodotto che è stato realizzato nel settore manifatturiero e inviato al cliente. Che cosa ne sta facendo il cliente? In che modo si comporta? Quando richiede assistenza?
Tutti questi punti devono procedere insieme.
Queste fonti di dati formano il digital thread, la fabbrica connessa, il prodotto connesso o i digital twin, che sono la rappresentazione digitale di sistemi fisici. Ai clienti diciamo che devono iniziare prendendo il controllo di questi silos di informazioni esistenti che sono distribuiti nella loro catena del valore e che devono partire dai dati disponibili. È qui che vediamo piattaforme IoT giocare un ruolo cruciale, disaccoppiando il sistema di acquisizione dati quello delle attività umane ed eliminando la complessità dei sistemi aziendali esistenti, come per esempio l’ambiente ERP.
Solo collegando i dati di prestazione del prodotto con i dati di produzione e comprendendo la genealogia del prodotto è possibile pervenire alla visione centrale del prodotto: l’unione delle diverse fonti di dati offre i margini necessari per una visione perfetta del prodotto.
L’aggiunta dell’elemento umano
La comunicazione sicura, che permette uno scambio certo dei dati fra OT e IT, è la spina dorsale della digitalizzazione del settore manifatturiero. È un concetto ben assimilato fin dalla nascita dell’Industry 4.0, ma che rimane un’area di discussione aperta. L’OT deve alimentare l’infrastruttura IT. Per molti anni, l’OT è stato l’ambiente dei reparti di produzione, di dominio del personale di fabbrica. Lo si configurava, lo si avviava e venivano creati dei prodotti: questa era la sua responsabilità. Oggi, l’OT deve comunicare in modo continuo ed efficace in ottica di network con l’intero sistema aziendale. È necessario saper portare i dati OT nel mondo IT. Attività complessa perché vi sono certe considerazioni di rete e certi aspetti di sicurezza che non sono necessariamente ben noti all’organizzazione IT ma che sono utilizzati dal lato OT per proteggere le apparecchiature. Quando parliamo di convergenza IT/OT, ciò che vediamo tipicamente sono degli ambienti che devono estrarre con difficoltà i dati dai reparti di produzione e portarli allo strato IT superiore.
Il futuro dei dati
L’edge computing è un concetto che è cresciuto nel suo significato, man a mano che i produttori hanno intrapreso la strada verso un futuro digitale e che è integrato nella gestione dei dati. Esso permette ai produttori del settore manifatturiero di elaborare e filtrare localmente i dati per ridurre la quantità inviata a un server centrale, che sia in azienda o su cloud. Nel suo stato attuale, Industry 4.0 ha alcuni blocchi considerevoli, che ne ostacolano il successo. L’edge computing è la soluzione per superare molti di questi ostacoli.
PTC, ad esempio, ha recentemente incontrato un cliente, esaminando diversi casi d’uso attinenti il suo reparto di produzione. La discussione verteva sul fatto se avesse senso potare i dati verso un datacenter, piuttosto che elaborarli subito, vicino alla fonte. In molti casi, ciò dipende dalla necessità tipiche dei reparti di produzione. Se si deve fare un controllo statistico di processo, la frequenza richiesta e la correzione della causa è molto elevata: si acquisiscono e si elaborano dati decine e forse anche centinaia di volte al secondo. In questo caso non esistono prerogative in termini di ampiezza di banda o latenza che permettano di inviare le informazioni a un datacenter, ovvero di ottenere una risposta certa e di poterla mettere in atto senza investimenti significativi.
Questo è un esempio perfetto nel quale l’edge computing è la soluzione più adatta. Nello stesso tempo, vi sono moltissimi altri casi d’uso nei quali il ricorso a strutture di datacenter è preferibile.
Proseguendo l’analisi, la capacità di raccogliere tutti questi dati in una sola location accelera senza dubbio la capacità di elaborare, e quindi ottenere, informazioni dai dati stessi: il lavoro di business intelligence vede nel cloud o nel data center una soluzione idonea. Tuttavia, il prossimo passo importante per un’azienda, dal punto di vista dell’ingegneria connessa con il PLM e dal punto di vista di un ambiente CAD, è quello di utilizzare concretamente i dati. È interessante il fatto che i reparti di ingegneria e produzione del settore manifatturiero saranno probabilmente fra gli ultimi ad adottare le capacità cloud, ma questo è dovuto principalmente a questioni di sicurezza di dati e IP. In futuro, però, ciò diventerà molto interessante per tutti coloro che hanno un’iniziativa di digital thread all’interno delle loro aziende in funzione delle elevate caratteristiche di flessibilità, scaling e configurazione.
di Paolo Delnevo, Vice President PTC Southern Europe